Repair Information
Does Your Foundation Need Repair? Cracks in Your Walls Cracks in your walls are not only unsightly, but they are often a sign of more severe underlying problems. Depending on several factors such as size, extent of damage, cause, and method of correction, crack repair can either be as simple as an injection in the […]
Underpinning Foundations
What is Foundation Underpinning? Underpinning is the process of strengthening the foundation of an existing home or building. Intech Anchoring Systems network of certified installing contractors utilize the process of underpinning by installing a pier system (either helical or resistance) to make your foundation structurally stronger. This can take a variety of forms: extending your […]
Sinking Foundation
What is a Sinking Foundation? A sinking foundation is a problem encountered by thousands of homeowners every year. To spot a sinking foundation, first be aware of the key signs. Concrete that has cracks that appear above ground level may indicate that your foundation has settled unevenly, lower on one side than the other. The […]
Your Leading Supplier of Foundation Solutions and Foundation Repair Products
Contractors across all markets face a litany of challenges in addressing, repairing, or restoring foundation problems. We are the regional distributor for several of our industry’s leading brands, including Magnacore and CHANCE. Looking for Foundation Solutions and Foundation Repair Products? The construction market is full of qualified experts all competing for the same work and […]
Supplying Contractors in Residential Home Foundation Repair
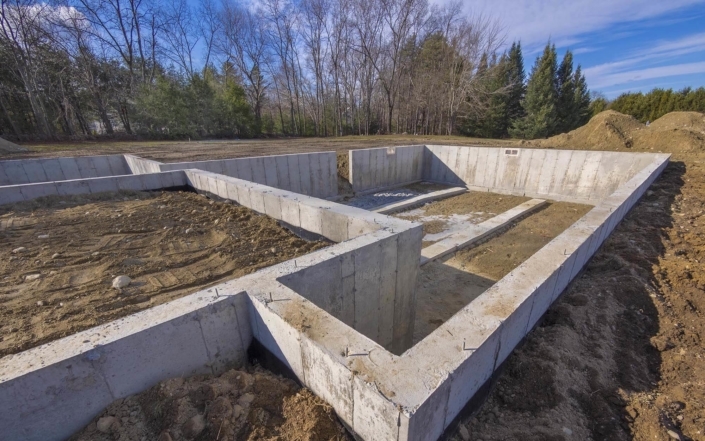
Intech offers industry-leading installation equipment and represents the top market brand names for your residential home foundation repair supplies. You can rely on our knowledge and years of experience in foundation repair products and solutions. An Experienced Material Supplier Makes the Difference When It Comes to Foundation Repair For the past 20 years, Intech Anchoring […]
Supplying Contractors specializing in Home Foundation Repair
Intech Anchoring offers industry-leading installation equipment and represents the top market brand names for your residential home foundation repair supplies. You can rely on our knowledge and years of experience in foundation repair products and solutions. An Experienced Material Supplier Makes the Difference When It Comes to Foundation Repair For the past 20 years, Intech […]
The Benefits of Commercial Concrete Repair and Restoration
For some, concrete repair and restoration might seem like a purely aesthetic decision. No one wants their property or floors to look like they are in bad condition, but the truth is that concrete repair products offer more benefits than just restoring the appearance of your surfaces. Cracks in the concrete affect the safety of […]
Engineering Support from Product Distributors
When choosing Intech Anchoring Systems as your distributor, you gain the advantage of having our dedicated engineering team readily available to provide the necessary support and expertise. We understand the importance of providing assistance and guidance throughout your projects, ensuring that you have the knowledge and resources needed for success. Engineering Support Solutions Intech understands […]
Which One to Choose: Hollow Bar Micropiling or Solid Bar?
A micropile is a top-down operation using a single metal bar with a cement grout mixture to create a strong foundation for buildings or earth retention. Micropiles are small in diameter, ranging from a single inch to less than five, and are drilled into the ground and grouted with cement. A micropile is typically reinforced […]
WHY CONTRACTORS SUCCEED WITH EXPOXY CRACK REPAIR
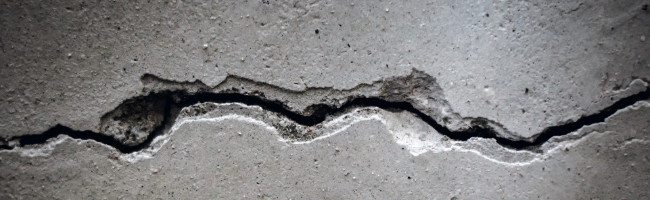
There’s an easier way to fill that crack – it’s with an epoxy crack repair system. Partner with us and learn the prime route for epoxy injections